Manufacturing
From ensuring weld quality to detecting surface flaws in metal components, our certified experts deliver precise non-destructive testing (NDT) solutions that enhance product reliability, maintain compliance, and optimize production processes.
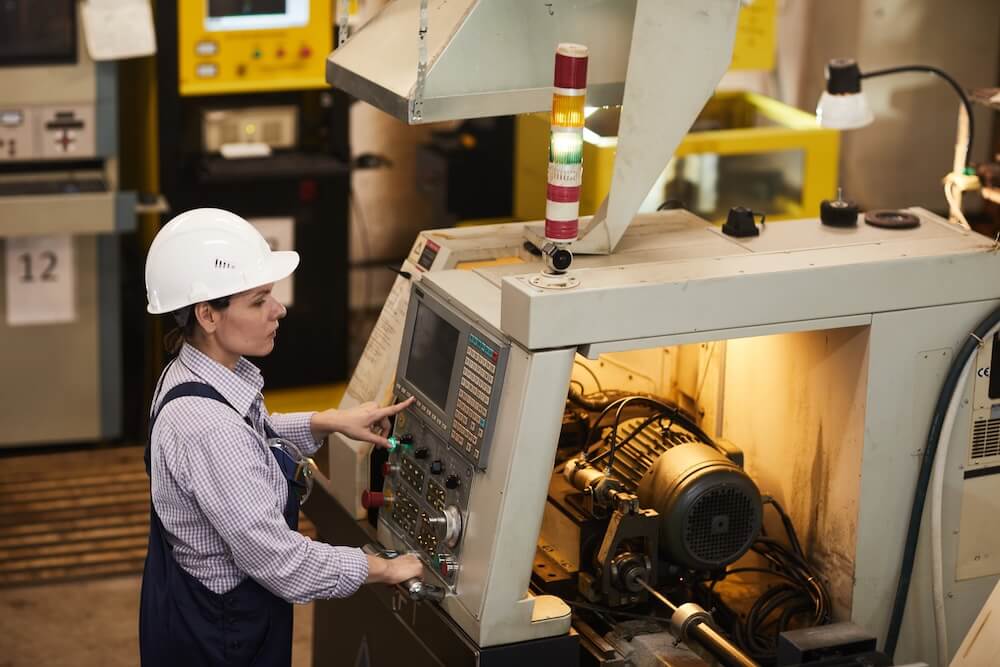
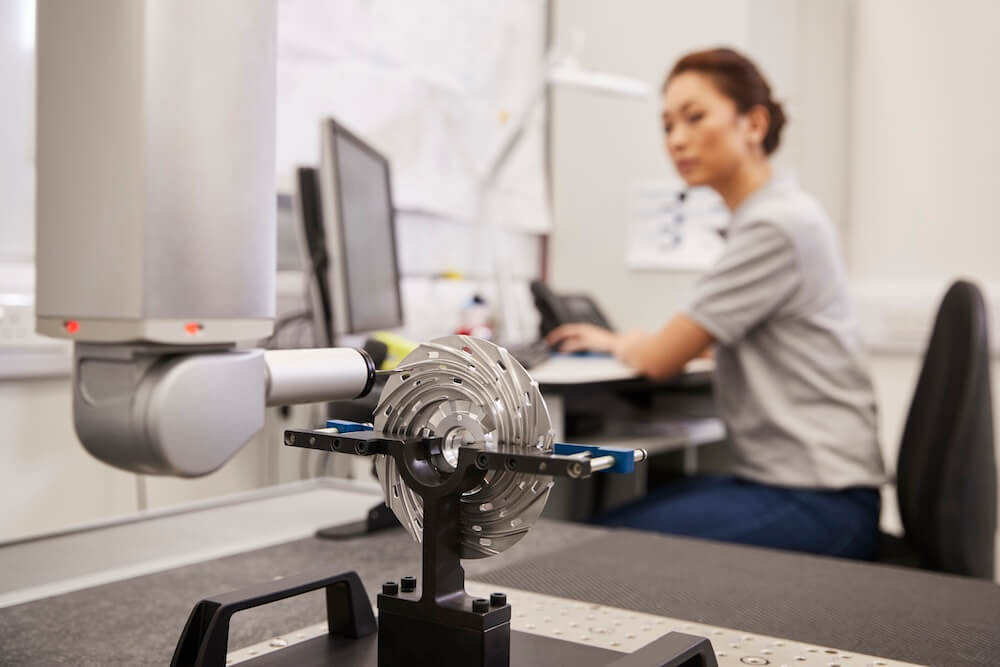
Ready to Ensure the Integrity of Your Assets?
Partner with Boomer Technical Resources for reliable, precise, and non-destructive testing services tailored to your needs.