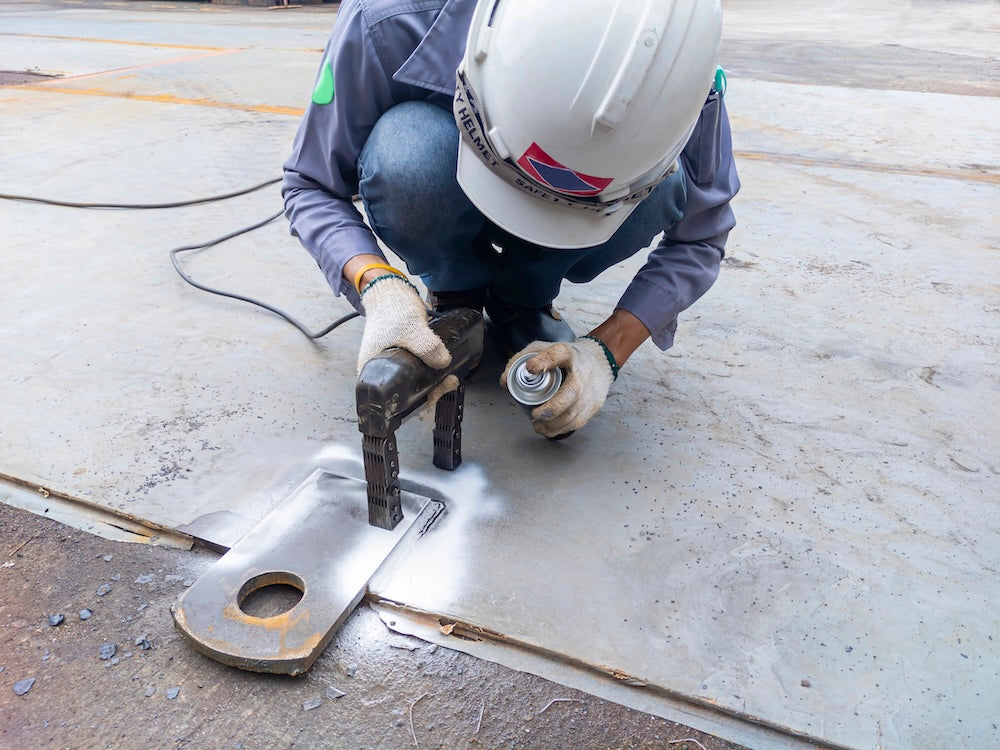
Understanding the Difference Between Destructive and Non-Destructive Testing
Testing is a vital process in assessing the quality and reliability of materials and structures across industries. Among the various methods, destructive and non-destructive testing stand out as primary approaches. Understanding these techniques and their applications is crucial for selecting the right one based on your needs.
What Is Destructive Testing?
Destructive testing involves evaluating a material or component by subjecting it to conditions that lead to its failure or irreversible damage. This method helps to understand the strength, durability, and performance limits of a specimen. Common destructive tests include:
- Tensile Testing: Measures the maximum load a material can withstand before breaking.
- Impact Testing: Evaluates material toughness by subjecting it to sudden forces.
- Hardness Testing: Determines resistance to deformation under a concentrated load.
The critical drawback of destructive testing is that the specimen becomes unusable afterward. However, this method provides essential insights for safety-critical applications, such as in aerospace or construction, where failure predictions are key.
What Is Non-Destructive Testing (NDT)?
Non-destructive testing, as the name suggests, evaluates materials and components without causing permanent damage. It is particularly useful when maintaining the usability of the tested item is important. NDT is widely applied in industries like automotive, oil and gas, and manufacturing to ensure safety and compliance without downtime.
Key NDT techniques include:
- Magnetic Particle Inspection (MPI): Detects surface and near-surface discontinuities in ferromagnetic materials using a magnetic field and ferrous ink.
- Liquid Penetrant Inspection (LPI): Locates surface defects by applying a penetrant liquid and a developer for visual detection.
- Radiography: Uses X-rays or gamma rays to detect internal flaws by capturing images on film or digitally.
- Ultrasonic Testing (UT): Employs high-frequency sound waves to locate internal discontinuities and determine their depth.
- Thermography: Detects thermal anomalies, such as hot or cold spots, which may indicate structural issues.
Key Differences Between Destructive and Non-Destructive Testing
Aspect | Destructive Testing | Non-Destructive Testing |
Purpose | Determines failure limits | Ensures quality and detects flaws |
Specimen Use | Specimen is damaged or destroyed | Specimen remains intact |
Applications | Research and safety-critical evaluations | Routine inspections and maintenance |
Cost | Higher (due to specimen loss) | Cost-effective for ongoing operations |
Choosing the Right Method
The decision between destructive and non-destructive testing depends on factors such as the material's purpose, testing objectives, and budget constraints. While destructive testing offers in-depth insights for development phases, NDT ensures continued usability, making it ideal for operational settings.
By understanding the differences and applications of these testing methods, industries can implement more efficient quality assurance processes, enhancing safety and reliability.
How Non-Destructive Testing Keeps Formula 1 Cars Safe and Fast Read More